Key principles of Continuous Improvement
The continuous improvement methodology is a systematic and ongoing approach to enhancing products, services, processes, or practices.
The fundamental principle behind continuous improvement is the organisational-wide pursuit of incremental and sustainable enhancements rather than large disruptive overhauls.
In addition to incremental enhancements, the continuous improvement methodology places importance on customer centricity, data-driven decisions and cyclical iterative processes.
Organisations are encouraged to put the needs of customers at the centre, set goals, implement changes, measure outcomes and repeat the cycle over and over again. Each iteration builds upon the lessons learnt and improvements achieved from the previous one.
Continuous improvement methodologies and tools are widely used in various industries. Some of the most popular methodologies include Plan-Do-Check-Act (POCA), Kaizen, Lean, Six Sigma, TQM, and Agile.
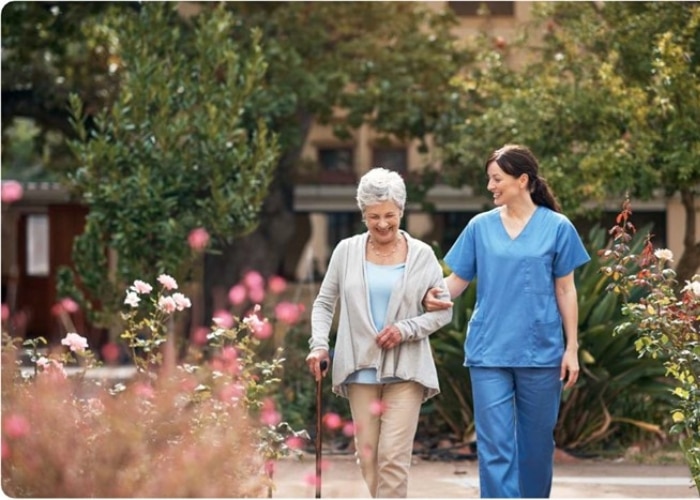
Implementing Continuous Improvement in Care
Implementing Continuous Improvement in Care requires a systematic and multi-faceted approach. Here are some practical steps and strategies that we recommend:
ESTABLISH A CLEAR VISION AND PRIORITIES
Establishing a strong culture of continuous improvement requires leadership commitment to define a clear and compelling vision that is backed up by specific goals and priorities.
Candidates for continuous improvement initiatives should be sourced from a broad range of areas including:
• Regulator audit outcomes and assessments
• Internal audits and inspections
• Incidents, hazards and near misses reported
• Client and staff feedback
• Business strategy and objectives
To prioritise, we recommend evaluating each initiative within a prioritisation matrix based on the impact on customer and business outcomes. In doing so, it is critical to keep the most important principle of Continuous Improvement front of mind at all times: the focus on incremental and ongoing enhancements NOT large disruptive overhauls.
ADOPT AND TRAIN STAFF ON A CONTINUOUS IMPROVEMENT FRAMEWORK
At Riskteq, we recommend the Plan-Do-Check-Act (PDCA) continuous improvement framework. It was developed by Dr. W. Edwards Deming, a renowned statistician, professor, author, lecturer, and consultant who made significant contributions to the field of quality management. This framework is also recommended by the Aged Care Quality and Safety Commission.
The PDCA cycle consists of four main stages, which should be executed in a cyclical manner:
- Plan: In this stage, the organisation identifies a problem or an opportunity for improvement. This planning phase involves determining what needs to be done, who will do it, and how it will be accomplished.
- Do: After the planning phase, the organisation implements plans by executing specific actions and changes.
- Check: Once actions are implemented, the organisation collects and analyses data to evaluate results. This step involves measuring outcomes against the goals and objectives set in the planning phase. It helps determine whether the changes have led to improvements or if further adjustments are needed.
- Act: Based on the analysis of data in the “Check” phase, the organisation makes informed decisions about the next steps. If results are satisfactory, improvements may be standardised and integrated into regular operations. If the results are not as expected, the organisation will act to refine the plan, make necessary adjustments, and repeat the cycle to drive further improvement.
REPEAT
As the Act phase concludes, transition seamlessly into the planning phase for the next POCA cycle. Based on the outcomes and lessons learned, set new objectives, refine strategies, and plan for further improvements. This cyclical approach ensures that the organisation is continually advancing in its pursuit of excellence.
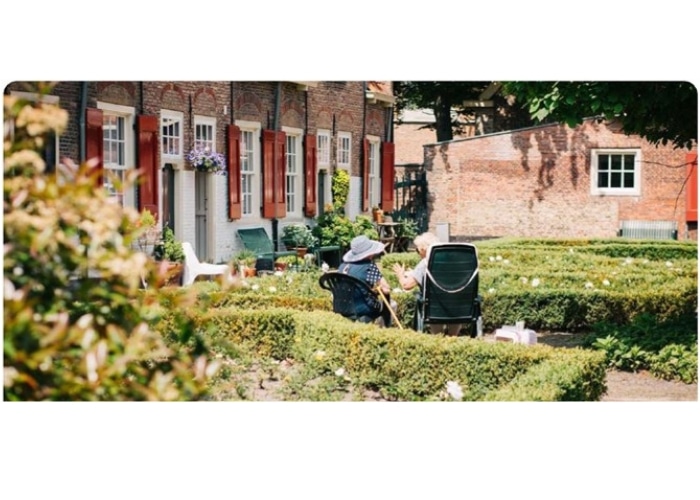
Riskteq software for Continuous Improvement in Care
Riskteq software enables customers to build an integrated continuous improvement system to enhance the quality of care. It is built from the ground up to implement POCA continuous improvement workflows with an established track record in the Australian Care industry:
- Shortlist continuous improvement candidates based on defined business objectives, internal assessments, surveys, stakeholder feedback, inspections and incident data.
- Define SMART objectives linked to business goals.
- Create specific action plans linked to each objective with assigned action owners.
- Set up automated alerts, reminders, & escalations to notify users regarding relevant actions, updates, or activities.
- Record and track staff skills, competencies, licences, qualifications and registrations. Use templated work plans to guide the selection of appropriately skilled people for each task.
- Build proactive feedback channels through digital forms and questionnaires that are accessible from any device.
- Integrate systems and centralise data to build a single view of quality and continuous improvement plans across all facilities.
- Allocate assets and equipment to appropriate staff. Manage safety inspections and pre-start checklists. Flag damaged equipment. Schedule servicing and maintenance activities.
- Leverage comprehensive dashboards and drill-down reports to identify trends and areas for improvement and set benchmarks for performance.
- Implement automated alerts and triggers for early detection of emerging trends or potential problems.
- Build site profiles for all key Care locations (including private residences) complete with historical trend analysis of incidents, hazards, risks and improvements.
- Manage incidents and near misses, triaging each item using a standard incident matrix. Record personnel involved, witness details, any equipment that was damaged and remediation plans.
- Document lessons learnt and communicate results.
RISKTEQ’S APPROACH TO MANAGING CHANGE
Although new processes or technology may be involved, the efficacy of any continuous improvement initiative hinges entirely on individuals and their capacity to comprehend and endorse the associated changes. Passive resistance has the potential to undermine even the most well-intentioned programs. Consequently, engaging individuals in the transformative process is paramount for success. Riskteq’s human-centric approach to continuous improvement emphasises clear communication, adept stakeholder management, and facilitating a comprehensive understanding of the vision’s value for both individuals and the organisation.
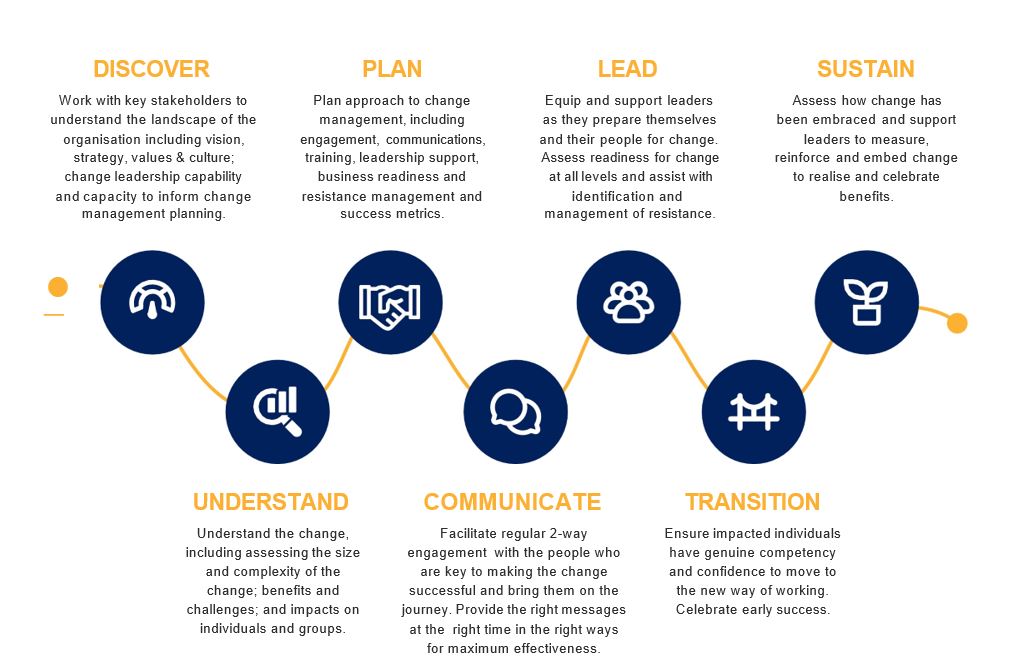
About Riskteq
Riskteq’s integrated Risk, Safety and Quality management platform empowers organisations with the digital tools required to drive risk-based management and client-centred planning into their business-as-usual culture.
Proudly made in Australia, we enable organisations to link business objectives like high quality of service with risk prevention, incident management, feedback and continuous improvement initiatives.
Visit Riskteq at riskteq.com today.